News
It shouldn’t shock you to read that hydraulic fluid is the lifeblood of the hydraulic pump, hydraulic reservoir, and perhaps most importantly the hydraulic motor on your Hydra-Tech submersible dewatering pump. Which hydraulic oil should you choose to fill the reservoir on your new hydraulic power unit? Whether you’re using a 6 horsepower or a 400 horsepower HPU, the choice of hydraulic oil is the same for both (but the volume required to fill it will vary significantly.
For Hydra-Tech’s smallest gas and diesel hydraulic power units of less than 15 horsepower, use Dexron ATF. This hydraulic oil offers a wide temperature range and excellent wear properties.
All hydraulic power units greater than 15 horsepower require AW46 hydraulic fluid in the reservoir and lines. This hydraulic oil has anti-wear additives (AW) and is designed for normal climates – it is 20 weight oil (ISO46). The number 46 is a viscosity value measured in centistokes. In colder climates, we recommend using 10 weight (ISO 32) or AW-32 hydraulic oil.
If you will be operating your HPU around lakes, streams or other environmentally sensitive areas you can fill the unit with environmentally friendly biodegradable hydraulic oil. Most manufacturers offer either a mineral based oil like Chevron CLARITY® or vegetable based oil like Mobil EAL224H.
Just like clean diesel is important for an engine, clean hydraulic oil is important to your hydraulic power unit. Simple steps such as wiping and cleaning quick disconnects with a clean rag can prevent dirt and debris from entering the hydraulic fluid system. Always follow the recommendations in the operator’s manual when it comes to service intervals related to the hydraulic system. In general:
- Change the hydraulic return line filter every 250 hours.
- Change the hydraulic oil every 600 hours (larger models can be 1000 hours).
- Every hydraulic reservoir has a suction strainer with an integral magnet to catch any metal that might get into the system. Any time you are changing the hydraulic oil and the reservoir is empty the suction strainer should be removed, thoroughly cleaned (including removing any metal debris from the magnet), rinsed / cleaned with mineral spirits and properly reinstalled.
These are some general suggestions for our whole hydraulic power unit range – consult your operator’s manual for the exact recommended service intervals for these critical hydraulic system components. Dirt or debris in your hydraulic system can damage or destroy major components like the hydraulic pump on the HPU as well as the hydraulic motor on your submersible pump. Hydraulic oil is the lifeblood of your Hydra-Tech Pumps system – make sure to keep it clean for a long and reliable service life!
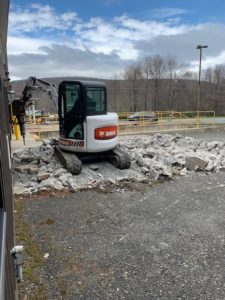
Continuing on with the product development theme, and referring back to the last blog post and the phrase “Necessity is the Mother of Invention”, here is another story of how one of our pumps came to be developed.
Sometime in early 1990 a customer contacted us looking for a pump to keep dust down on roads that lead in and out of orchards. During dry spells dust would be blown around from vehicle traffic on the dirt roads. The dust would then cover the fruit trees and cause problems. They had a truck with a boom that could extend out 40 feet and wanted to suspend the pump into an irrigation canal that ran alongside the road. They had hydraulics on the truck already, so they could use some of the existing hydraulic power to drive the pump. The pump needed to supply 200 GPM at 100 PSI so they could use a fire nozzle to spray water on the roads as they drove along. Also, the pump could not weigh more than 45 lbs.
Hydra-Tech Pumps had already developed the S3CHL pump (see the last blog post “We Listen Part 1”) but it weighed too much, was more powerful than they needed and required more hydraulic power than was available. The S3CML became a variation that has an aluminum body and requires less hydraulic power to drive it. It was a win/win for the customer and Hydra-Tech Pumps since this pump is now used in many other applications including aviation forest fire fighting (many portable fire fighting applications), barge and cargo ship dewatering, deep well dewatering, tank stripping, irrigation, piling and dock jetting and other high head applications.
The S3CML is available in aluminum and only needs a maximum hydraulic flow of 16 GPM at 3500 PSI for full performance. But like the CHL, what performance you will get! This pump will deliver 460 gallons per minute with no head, but will still deliver 50 GPM @ 380’ of head! Again, just like the CHL, that is a lot of capability from a small pump.
“It pays to listen” and we hear you. Part of our job is to solve problems for customers. Sometimes the solution lies with a combination of existing products, sometimes the solution involves a referral to someone else’s product, and sometimes the solution needs to be developed. Do you have any challenging applications that we can help you solve?
I’m sure you have heard the term “Necessity is the Mother of Invention”. For us at Hydra-Tech Pumps it means we are always listening to our customers’ needs and requests for pumps and hydraulic power units that will meet specific requirements. Most of the time this means offering the right combination of hydraulic submersible pump and hydraulic power unit to address a challenging application. Once in a while it leads to something else.
Sometimes these ideas or challenging applications result in the development of new products that we can offer as a standard product. One case in point is the S3CHL pump. Sometime in 1987 a customer in Jacksonville Florida approached Hydra-Tech Pumps looking for a pump that would provide flows over 400 GPM, discharge pressures up to 175 PSI, fit into a 12” deck opening, portable enough to be carried by one person and handle a wide range of water and oil mixtures. This pump would be used for tank stripping and emergency tank transfer on tanker ships. We developed the S3CHL pump to do just that and more. This pump has found its way into other applications such as firefighting, deep well dewatering and irrigation.
The S3CHL is available in aluminum or ductile iron and needs a maximum hydraulic flow of 30 GPM at 3500 PSI for full performance. But what performance you will get! This pump will deliver 500 gallons per minute with no head, but will still deliver 50 GPM @ 420’ of head! That’s a lot of capability from a small pump.
“It pays to listen” and we hear you. Part of our job is to solve problems for customers. Sometimes the solution lies with a combination of existing products, sometimes the solution involves a referral to someone else’s product, and sometimes the solution needs to be developed. Do you have any challenging applications that we can help you solve?
Hydra-Tech Pumps’ building expansion project is getting real as the steel for the addition was delivered last week – the prep work is close to done and the excavation will begin soon. We have teased this in past newsletters but now it is full steam ahead!
We wanted to tell you the story behind the current building and the need for this additional space. When Hydra-Tech was purchased from the original owners in 2005, the plan was to move it to Nesquehoning, PA where the new owners operated another manufacturing business. After considerable searching for a suitable building, the decision was made to buy an existing building, less than 10 years old that was built as a catering facility and restaurant / bar which held special events such as holiday parties and weddings. You can imagine the amount of work that went into converting the space from this kind of business to a light manufacturing facility to accommodate the welding, fabrication, machining, assembly, painting, inventory storage and other requirements to operate Hydra-Tech Pumps. Considerable work was put in and Hydra-Tech Pumps moved into our current building in September of 2007.
The building has served us well for almost 12 years and we have made many adaptations and improvements along the way to accommodate our growth and manufacturing requirements. However with our growth we have simply run out of room. Putting up an additional 8000 square feet will be a huge help. The other benefit we will get from this project is moving our test tank indoors. We will put more frequent updates on social media and keep you posted on our progress in future newsletters as well.
Any well-built hydraulic power unit (HPU) includes a system pressure gauge on the high pressure side. When this HPU gets paired with a hydraulically driven submersible pump, the readings on that gauge can both help the operator reach the best operating point (given current conditions) and assist in analyzing a problem situation when the submersible pump is not moving water.
Finding the Best Operating Point:
In many parts of life, more is better, but when it comes to operating an engine based hydraulic power unit, that is not the case. By using the pressure reading it is easy to find the sweet spot for any particular pumping situation. Specifically, the pressure shown on the gauge is an indication of the amount of work being done by the hydraulic motor on the pump head. The higher the pressure, the harder the motor is working. This working pressure profile can vary for different styles of pumps, but the one thing that is the same across the board is this… when adjusting engine rpm the operator will see system pressure rising until it stops. When the needle stops moving, it means that given the current set up, the system is at its most efficient point. Attempting to increase engine speed in an effort to get more submersible pump flow will only result in burning more fuel; it will not change the gpm output of the head. Of course, as conditions change, that ideal point will change too, so further adjustments will be required to stay at the best spot. By educating your customers and staff about this pressure point, it becomes a win, win, as fuel costs can be cut, wear and tear on engines is reduced and the environmental impact of the fuel burn is minimized.
Problem Analysis Using System Pressure
Because hydraulic systems are fairly simple, they tend to react in the same way when something goes wrong. When using hydraulic power to drive a pump head, we look at three sides to the same problem to find the reason why the pump head is not moving water. If the submersible is not moving water, the operator should first note the pressure reading shown on the gauge on the high pressure side of the system.
If the pressure is above 1000 psi and you can be sure that the pump impeller is turning, then the following conditions are likely preventing the pump from moving product:
- Head conditions are too great for the pump to overcome and a different pump head/HPU should be employed
- The discharge line is kinked, or somehow blocked downstream of the discharge or too much lay flat hose is choking off pump head discharge flow
If the pressure is above 1000 psi and the impeller is not spinning, then the following conditions are likely preventing the pump from moving product:
- The bearings or hydraulic motor are seized and need to be repaired
- The impeller is jammed and the top of the pump may need to be removed to clear the obstruction
If the pressure is below 1000 psi look at the following:
- Dead head the hydraulic power unit and see if it alone is capable of developing 2000+ psi ( FAQ –Is there a quick way to determine if my power unit is providing sufficient flow/pressure?)
- If the HPU is good, the next thing to check for is lack of water in the pump. Is the suction opening and/or the strainer base clogged?
- If the suction is not clogged, the pump may not be submerged enough to begin working. Generally speaking the pump should be in water that reaches to the bottom of the hydraulic motor.
- Once you know if the HPU is good, and the suction side is clear and the pump is submerged enough, it is possible that the pump is air bound. This can even occur with a pump that is continually sitting in water.
- To overcome this problem, check the vent bolt on vortex impeller pumps to see if it clear. This vent bolt is an air escape;
- Pull the pump from the water and before lowering it back down, lay it on its back with the discharge at 12 o’clock,
- Then lower into water
- Pull the pump back out, start the power unit and have the impeller turning when dropping it back in
- If none of the above are true, then it is likely worn parts. The hydraulic motor could be washed out and the oil when under pressure is blowing by instead of doing the work. Or, there may be excessive wear at the impeller and internal parts which is greatly reducing the efficiency of the pump head.
- To overcome this problem, check the vent bolt on vortex impeller pumps to see if it clear. This vent bolt is an air escape;
While troubleshooting can sometimes be a headache with hydraulic pumping systems, going through the process detailed above usually uncovers the cause of the problem. If it does not, feel free to call us, and a member of our staff will be happy to work through to a solution.
Check out the support tab on our website for other useful technical information about our pumps and hydraulic power units.
How much time do you spend on the road or on your commute? How many businesses do you regularly drive by and ask yourself “I wonder what they do in there?” For some members of Hydra-Tech Pumps’ local business community, that question was answered during an event this week. Employees of a number of different businesses are a part of a “Leadership Carbon” class, through the Carbon County Chamber (Of Commerce) & Economic Development Corporation, did a tour of some local manufacturers including Hydra-Tech Pumps. The group visited three companies. The first company manufactures molds for the concrete sound barriers that you see along the interstate, the second company receives and cleans / treats hazardous materials, primarily needles and other medical waste items. The last stop was a visit to Hydra-Tech Pumps.
After a short history and question and answer session we hit the shop floor for the nickel tour. The first stop was the fabrication department where we cut raw steel and weld fuels cells and frames for our electric, diesel and gas Hydraulic Power Units. We worked our way through the production floor past the paint booth where we paint all of our pumps and power units. We saw the final assembly and test area where HPUs are set and tested for proper performance, and every pump is run before it leaves the building. The group was impressed with the sight of our new S30M axial pump and HT400DJV power unit, just back from successful offsite testing for certified curves.
We stepped out of the back of the building for a peek at the sandblasting operation and to see the long line of HPUs ready to be shipped to customers. Back inside we went through the pump assembly department, inventory area and looked into the machine shop where raw castings are converted into finished parts. After the tour there were more good questions before the group departed. For this group of local business people, we answered the question of “What do they do in there?” They finished their day with a better idea of what some of the local manufacturers produce and where in the country and the world that product ships.
For our colleagues, customers and vendors, we enjoy giving the tour and have had the pleasure in our 11 years at this location of welcoming and entertaining visitors from near and far. At the end of October we welcomed our Russian distributor here for a couple of days. A customer called yesterday and reminded me that he had been here (from Indonesia) to visit near the end of 2012. If you’re ever going to be in or around northeast PA and have time for a visit please let us know – we would be happy to show you what we do here in Nesquehoning.
If your company / rental location has Hydra-Tech Pumps in your arsenal, then you probably have a shop where the pumps and hydraulic power units can be serviced and maintained. If hydraulic power units and pumps are new to your organization, what are some of the basic tools that should be on hand to properly troubleshoot and service a hydraulic power unit?
In addition to a basic set of mechanic’s hand tools, a good standard and metric Allen wrench set, pipe wrenches, and clean rags are helpful to have available. Making repairs and doing periodic maintenance to a hydraulic power unit is important and both the service interval recommendations supplied by the engine manufacturer and Hydra-Tech Pumps should be followed closely to insure long life for your HPU.
When it comes to hydraulic power unit set up or troubleshooting, the most important tool that you can have on hand but probably can’t buy locally is a good flow control / flow meter setup. A flow control / meter will allow you to properly test the hydraulic flow of your hydraulic power unit, make adjustments to the hydraulic flow, and allow you to temporarily affect the hydraulic flow and pressure if you had hydraulic pumps or tools that you wanted to test in your shop. Without it you are only able to determine what pressure you are producing through the hydraulic pump coupled to the engine – not the gallons per minute of flow you are getting. This is especially important if you have a variable volume piston pump and want to make adjustments to the flow at a pressure that the HPU is delivering to your submersible pump / hydraulic tools. If you provide too much hydraulic flow to hydraulic motors on tools or pumps, you will most likely damage the motor.
Pictured: Flow Meter Control for 1” connection 0-32 GPM 0-5000 PSI.
Pictured: Close up of 0-32 GPM Flow Gauge and 0-5000 PSI Gauge.
Here are a few things you can do with a flow meter / flow control setup that you cannot do without it:
- The tool / test set shown above allows you to run a loop of hose from the pressure fitting on the reservoir back to the return fitting with an inline flowmeter. With this you are able to see the hydraulic flow and pressure that the HPU is producing. This benefits you in two ways:
- Very basic but helpful, you can verify the max performance (how it is set up – flow and pressure at full throttle) of a power unit. In the rental world, this is especially important if you have received an HPU from another branch.
- If your unit has a hydraulic pump (variable volume piston pump) that allows adjustment, you can change hydraulic pump settings (how the HPU is set up for flow at a pressure) and have instant feedback on the changes that you are making. Some customer will buy a single power unit for two different pumps with two different hydraulic requirements and will change the set up on the HPU depending on which pump they need for the job.
- You are also able to use this device inline to adjust the flow up or down, or simply use it to see what affect changes in the throttle setting of the engine have. The flowmeter allows you to see changes in hydraulic flow (and pressure can be noted on the gauges) as you increase or decrease the throttle on any power unit. For example, the flow control would allow you to see what impact to the flow running an HT13G at half throttle would have.
- You can troubleshoot an HPU more effectively with this tool to determine that in addition to building pressure, your unit is providing hydraulic flow to the devices it is meant to power. One of the challenges we have when helping a customer to trouble shoot a problem with a system (pump and power unit) is verifying hydraulic flow (and as a result, hydraulic pump function). This device allows Hydra-Tech and our customer to verify that the HPU is producing hydraulic flow and isolate the problem with the device you are powering.
Hydra-Tech pumps can put together a setup appropriate for the hydraulic power unit(s) you will be working with. Call today for more information, you will quickly find that when it comes to preventative maintenance as well as other tasks related to your HPU this will be the most valuable tool in your “hydraulic” tool box.